Impact of Pressure and Rotational Speed on the Efficiency of Dry Ice Blasting Machines: A Computational Fluid Dynamics Analysis
DOI:
https://doi.org/10.37934/ard.128.1.4763Keywords:
Dry ice machine, computational fluid dynamics, pressure change, rotational speed changes effectAbstract
Dry ice cleaning machines have become a highly effective solution in industrial cleaning, utilizing dry ice pellets to remove contaminants without damaging surfaces. This method, known as dry-ice blasting, uses compressed air to propel dry ice pellets, offering a cleaner alternative to traditional chemical and high-pressure water jet methods. The performance and effectiveness of dry ice cleaning machines are largely determined by the flow dynamics of the dry ice as it interacts with the cleaning surface. This study uses Computational Fluid Dynamics (CFD) to analyze the impact of operational parameters, specifically on rotational speed changes effect of gear and pressure inlet settings. The rotational speed are tested at 100, 250, and 500 rotational per minutes (rpm) to observe its effect on flow, while pressure variations of 8, 10, and 12 bar were examined to understand their influence on fluid behavior, ultimately enhancing machine efficiency and design. In conclusion, the analysis reveals that operating the dry ice machine at 250 rpm with an inlet pressure of 12 bar offers the best performance. This combination results for 12 bar shows 9.13% increament in exit velocity, reaching 1269 m/s compared to 1159 m/s at 10 bar. The nozzle pressure also increases by 17.66%, from 556.1 kPa to 654.3 kPa, ensuring stable flow dynamics. Additionally, the turbulent kinetic energy (TKE) rises by 19.62% to 43,770 m²/s², improving particle mixing and distribution. This optimal setting enhances machine efficiency and effectiveness, making it the ideal choice for dry ice spraying operations.
Downloads
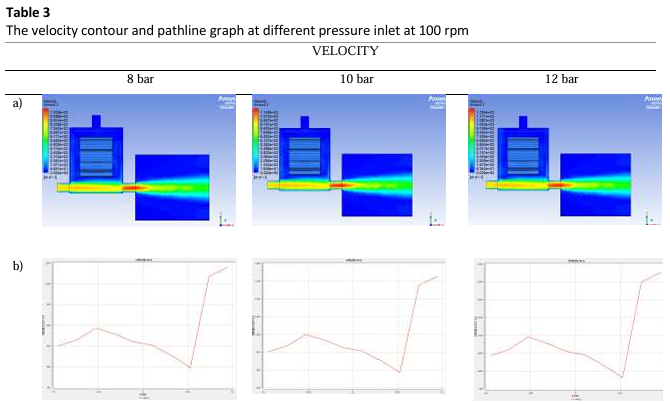