Different Reshaping Methods of Clinched Joints to Reduce the Protrusion Height
DOI:
https://doi.org/10.37934/ard.134.1.134148Keywords:
Clinch process, mechanical joining, FEM, sheet metal, protrusion height, reshapingAbstract
The widespread adoption of mechanical clinching technology is hindered by its drawbacks, with the most prominent being the protrusion above the sheets in conventional clinched joints. This protrusion creates a raised bump on the sheets, rendering the use of conventional clinching impractical in visible areas where a flat surface is required. The application of mechanical clinching could be limited due to the outward bulge on the surface of the sheets, which can impact the performance of the joints. To overcome this issue, this study seeks to identify a technique for decreasing protrusion height while simultaneously enhancing the strength of clinched joints. Indeed, a reshaping method for clinched joints has been employed, including the utilization of reshaping rivets, to effectively reduce the protrusion height and enhance the joint strength. The investigation of the reshaping process will be conducted, involving the creation of a finite element (FE) model for both the clinching process and the reshaping of clinched joints, utilizing LS-DYNA software. The FE model will be validated through experimental results to ensure its accuracy and reliability. The results show that the reshaping process reduces protrusion, but not strength. While reshaping with additional materials rivet and foam enhances material flow and joint strength. The rivet reshaping exhibits the highest compressive stress, indicating superior sheet metal strength.
Downloads
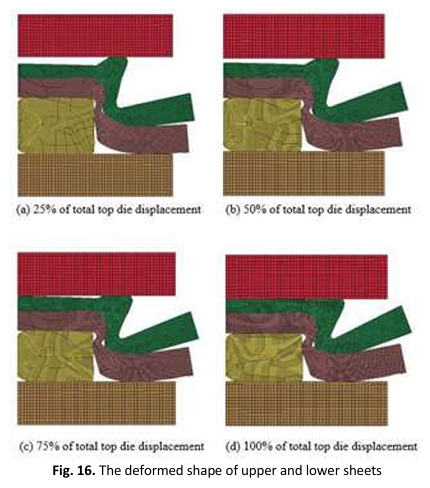