Payne Effect Prediction of Magnetorheological Elastomer by Krauss Model Comparing with Machine Learning
DOI:
https://doi.org/10.37934/ard.138.1.105115Keywords:
Magnetorheological elastomer, machine learning, neural network, viscoelastic behaviour, parametric modelAbstract
Magnetorheological elastomer (MRE) is having a complex viscoelastic behaviour especially when facing loading conditions such as different magnetic flux density and strain amplitude. Simple regression model such as least square regression and low order polynomial regression is unable to simulate such behaviour since the behaviour consists of linear and nonlinear portion. Hence, a parametric model namely Krauss model able to perform well on such behaviour specifically for viscoelastic materials. Thus, this work aimed to simulate the viscoelastic properties of MRE by applying Krauss model given four fitting parameters for each property where in this work, they are storage modulus and loss modulus, respectively. By following the trend of current research, a few machine learning models were also developed to simulate the behaviour to compare its performance with parametric model. The mentioned machine learning model were adopted including Guassian Process Regression (GPR), Support Vector Regression (SVR), Extreme Learning Machine (ELM) and Backpropagation Neural Network (BPNN). For both type of model structure consists of two inputs which were strain amplitude and magnetic flux density while two outputs which were storage and loss modulus. The results were analysed practically on the accuracy of prediction at linear region and nonlinear region of the viscoelastic properties. As the result, Krauss model exhibits 0.04171MPa of RMSE while among machine learning, ELM produced 0.00185MPa of RMSE for the highest magnetic field at linear region which achieved the smallest error among other machine learning. As the conclusion, it is noted that Krauss model as parametric model is computational burden when dealing with more variables. Meanwhile, machine learning model performance will keep improved when dealing with more variables. This can be one of the reasons on why machine learning kept utilizing in material properties prediction where it is significantly contributes to fasten the new material developments.
Downloads
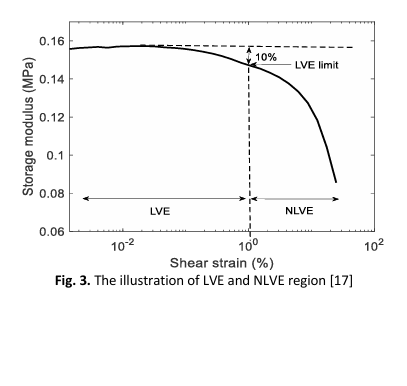