Composite Hydraulic Integration: A New Step Toward Lightweight Hydraulic Robots
DOI:
https://doi.org/10.37934/mjcsm.16.1.150166Keywords:
Hydraulic integration, Humanoid robots, Robotic arm, Assistive devices, Composite materials, Additive manufacturingAbstract
Normally, the use of hydraulics in humanoid robots is limited due to their design complexity, heavy weight, and high cost. This paper presents a new methodology for developing hydraulic integrated robotics system with lightweight, high strength, shorter production time and lower cost. This is achieved by combining the additive manufacturing of thermoplastic polymers and the simple forming of strong random fiber composites. A new methodology for fabrication of complex hydraulic integrated parts is explained in detail. The robotic arm of the humanoid hydraulic robot HYDROïD is chosen for implementing the new technique, specifically, the elbow lower part. A theoretical study for different possible 3D printing and reinforcement materials is presented. Then, an optimization method is presented to select the 3D-printed polymer material, the composite, the adequate sizes, and dimensions of the new arm part. Experimental validation and testing of the new part are presented. Moreover, PID gain scheduling controller (PID-GSC) is applied on the robotic arm during validation. The achieved results have shown that the new technique has led to significant weight reduction in the arm components to about 60% of the initial weight with a pressure tolerance of 150 bar. In addition, position tracking has been achieved successfully. Hence, the new attained solution has proved its worthiness with much lower cost and simple fabrication procedures.Downloads
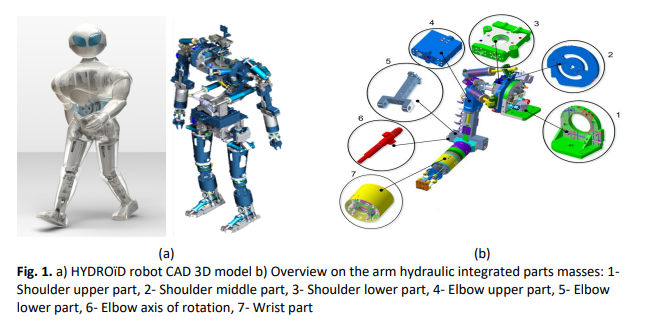